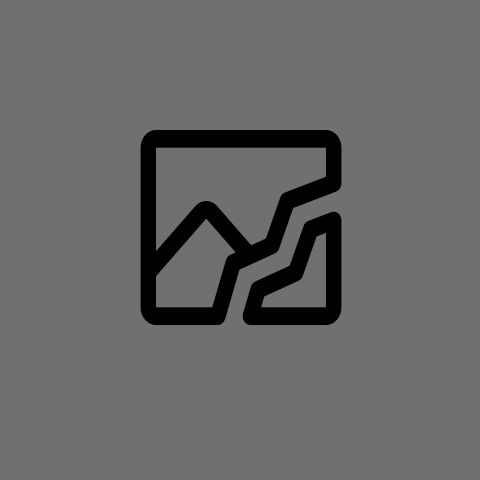
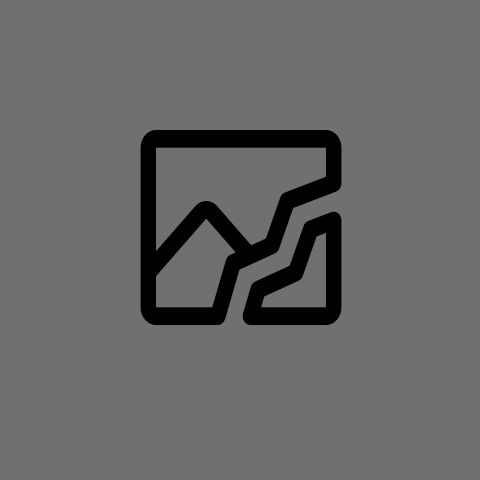
DRM on the resin combined with their high resin pricing is an issue. Heygears ABS-like is close to $90/kg while other ABS like are $25/kg.
Sadly this printer will never be a cost-effective solution with those jacked-up resin prices.
DRM on the resin combined with their high resin pricing is an issue. Heygears ABS-like is close to $90/kg while other ABS like are $25/kg.
Sadly this printer will never be a cost-effective solution with those jacked-up resin prices.
Recomendation?
The buildplate should fit to make it easy to use.
Software subscription and DRM on resin/filament are huge red flags. Had a look at heygears offerings as people describe it as the BambuLab equivalent for SLA. Looking into it, the feels more like a FormLabs company with overpriced resins and DRM to make you buy their resin.
Spending once 1.5-2k€ for the Flex RS printer is fine (more than I would like) but paying 40-70€/kg for resin killed it. Just not possible to economically justify paying twice as much for the source materials (resin). This would mean HeyGear jacking up the production cost by approx. 50-80%, indefinitely. A better option is it spend a day dialing in a third-party resin on the Prusa or Elegoo.
subscription = selling the same software indefinitely
paid upgrades = forced to deliver value/improvements with each paid update
for materials it is similar:
DRM = jacking up prices
open = competing on quality: You could use our first-party product with perfect integration but you are free to source whatever you like
Well, any printer will do that if you calibrate it well enough.
Pain point in the past where the build platform. Prints frequently failed because they would lift from the aluminum plate.
After a lot of trouble, I switched to a flexible buildplate which first was blasted with course “sand” followed by fine glass beans. flexplate so I can remove the print. The course surface makes the print stick but not stick too well. Would like this time to avoid all of this troubleshooting.
Also considered buying one of those printers that work upside down by projecting the light onto the surface and the print is lowered into the resin vat.
“Good” is fairly ambiguous here because what would a “good” slicer look like to you?
Good workflow (UI design), decent automatic support generation, good tool for manually brushing/configuring support material and ideally an elephant foot compensation setting/calibration for the first layer which has a significantly longer exposure time.
Support generation and being able to manually edit those pushed me toward PrusaSlicer.
The VAT tilt is a bit dangerous because of a potential resin leak of the release film, leaking into your printer’s internals
How big of an issue is that? Are there upgrades to seal the printer?
Back in the day, it was more or less a total economic loss for those cheap printers: LCD damaged, UV-array damaged and a complete mess within that was hard to clean.
I care about proprietary in the sense that I am locked to a certain slicer. Don’t care if the mechanical design and firmware is proprietary.
Also I don’t care that much about replacement parts. Affordable FEP-film (or those never versions of release film) is important. Other replacement parts are nice to have but never had to repair anything (the highest risk I see is flooding it with resin or dropping something in the vat that will crush the screen and if you are careful this is highly unlikely to ever happen especially now with the pressure detection on some printer models).
Great to hear you like it and that UV-tools work with it. What I hated about anycubic photon workshop was that the support generation was 100% manual (automatically created unusable results). PrusaSlicer was so much easier to work with.
The nice aspect of network connectivity is comfortably moving files to it and receiving a notification once the print is done.
I keep misplacing USB-sticks or it is a pain to first walk to the printer, picking up the stick, returing to the PC, and walking once more to the printer.
Bambu Lab A1 or even better the A1 mini.
You can get a plate swapper for the A1 mini. Combine this with an AMS for automatic filament changes (switching spools if one runs out) and you get a lights-out manufacturing solution: https://swap-systems.com/product/swapmod/
Do you mean with filament slicer a filament cutter?
The print quality is fine if the printer doesn’t freeze. Nothing exciting but also not bad for a $100 used device. Still, nothing to ride home about if $200 buys you a new BambuLab A1 mini. In sharp contrast is the Bambulab a reliable and superior printer in every aspect.
With this sad. If you still consider the Prusa Mini:
DO NOT update the firmware to versions with input shaping! They introduced a bug that you need to remove the SD-card before turning it on or otherwise the printer believes the firmware is damaged/bricked. This bug has been known for quite a long time without any fix from Prusa (present in multiple “stable”/release firmware versions!!!). I got rid of the last Prusa few years ago because of this issue so it might be fixed, might be still broken.
Do not rely on network connectivity/features. They are unstable meaning the printer needs to be restarted multiple times per day (combine this with the SD-card issue) and might freeze mid-print.